Video beschikbaar voor leden na onze kick-off op 30/03/2022.
5S wordt beschouwd als een fundamenteel onderdeel van het Toyota Productiesysteem, want zolang de werkplek niet zuiver en georganiseerd is, is het moeilijk om problemen en afwijkingen te zien en goede resultaten te behalen.
Een rommelige, onoverzichtelijke ruimte kan leiden tot fouten, productievertragingen en zelfs ongevallen welke de flow onderbreken en een negatief effect hebben op de klant leveringen. Door een systematisch georganiseerde werkplek te hebben, verhoogt een bedrijf de kans dat de productie precies zo zal verlopen als wat de klant vraagt
Soms gaat er bij 5S als tool te veel aandacht naar het ordelijke en zuiver houden van de werkomgeving. Vaak onder het moto “moet er mooi uitzien voor de baas of bezoekers” Echter 5S is veel meer dan dat, het gaat niet alleen om netheid of organisatie, maar het is een systematische vorm om afspraken met elkaar te maken . Afspraken die we met visueel management voor iedereen begrijpbaar en opvolgbaar maken. Zo gaan afwijkingen snel en voor iedereen duidelijk worden zodat men snel kan reageren en verbeteren. Het is dus de basis van standaard werk en continu verbeteren.
5S doe je dus voor jezelf , je team en voornamelijk voor de klant . 5S is een raamwerk dat de nadruk legt op het gebruik van een specifieke denkwijze en hulpmiddelen om efficiëntie en waarde te creëren. Het gaat om observeren, analyseren, samenwerken en zoeken naar verspilling en ook om de praktijk van het verwijderen van verspilling.
Laten we de verschillende stappen van 5S eens overlopen.
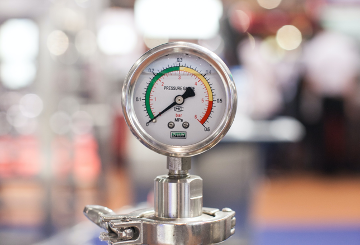
Seiri of Sorteren
Sorteren doen we om alleen de essentiële items die nodig zijn om taken uit te voeren te organiseren. Deze stap houdt in dat we samen de werkruimte evalueren om samen te bepalen wat nodig is en wat kan worden verwijderd. Alles wat niet wordt gebruikt om een werkproces te voltooien, mag/moet weg .
Enkele vragen die gesteld kunnen worden zijn:
- Wat is het nut van dit voorwerp?
- Wanneer werd dit voor het laatst gebruikt?
- Hoe vaak wordt het gebruikt?
- Wie gebruikt het?
- Is het echt nodig?
Deze vragen helpen om de waarde van elk voorwerp te bepalen. Een werkruimte is misschien beter af zonder overbodige spullen of spullen die niet vaak worden gebruikt. Deze voorwerpen kunnen in de weg staan of plaats innemen. Denk eraan dat het de medewerkers zijn die het beste in staat zijn om te beoordelen.
Als een groep heeft vastgesteld dat bepaalde items niet nodig zijn, overweeg dan de volgende opties:
- Geef de items aan een andere afdeling
- De spullen recyclen/weggooien/verkopen
- Artikelen in een warehouse opslaan
In gevallen waarin de waarde van een item onduidelijk is - bijvoorbeeld als een stuk gereedschap recent niet is gebruikt, maar iemand denkt dat het in de toekomst nodig kan zijn - gebruik een red tag labels of stickers om op de voorwerpte. Gebruikers vullen informatie over het voorwerp in, zoals
- Locatie
- Beschrijving
- Naam van de persoon die de tag aanbrengt
- Datum van aanbrengen
Vervolgens wordt het item in een "red tag area" geplaatst met andere dubieuze items. Andere collega’s en ploegen kunnen nu oordelen of zij het nodig ehbben. Als het voorwerp na een bepaalde tijd nog steeds in de red tag zone ligt is het tijd om het te verwijderen. Het is niet de moeite waard om dingen te bewaren die nooit worden gebruikt, want ze nemen alleen maar ruimte in beslag.
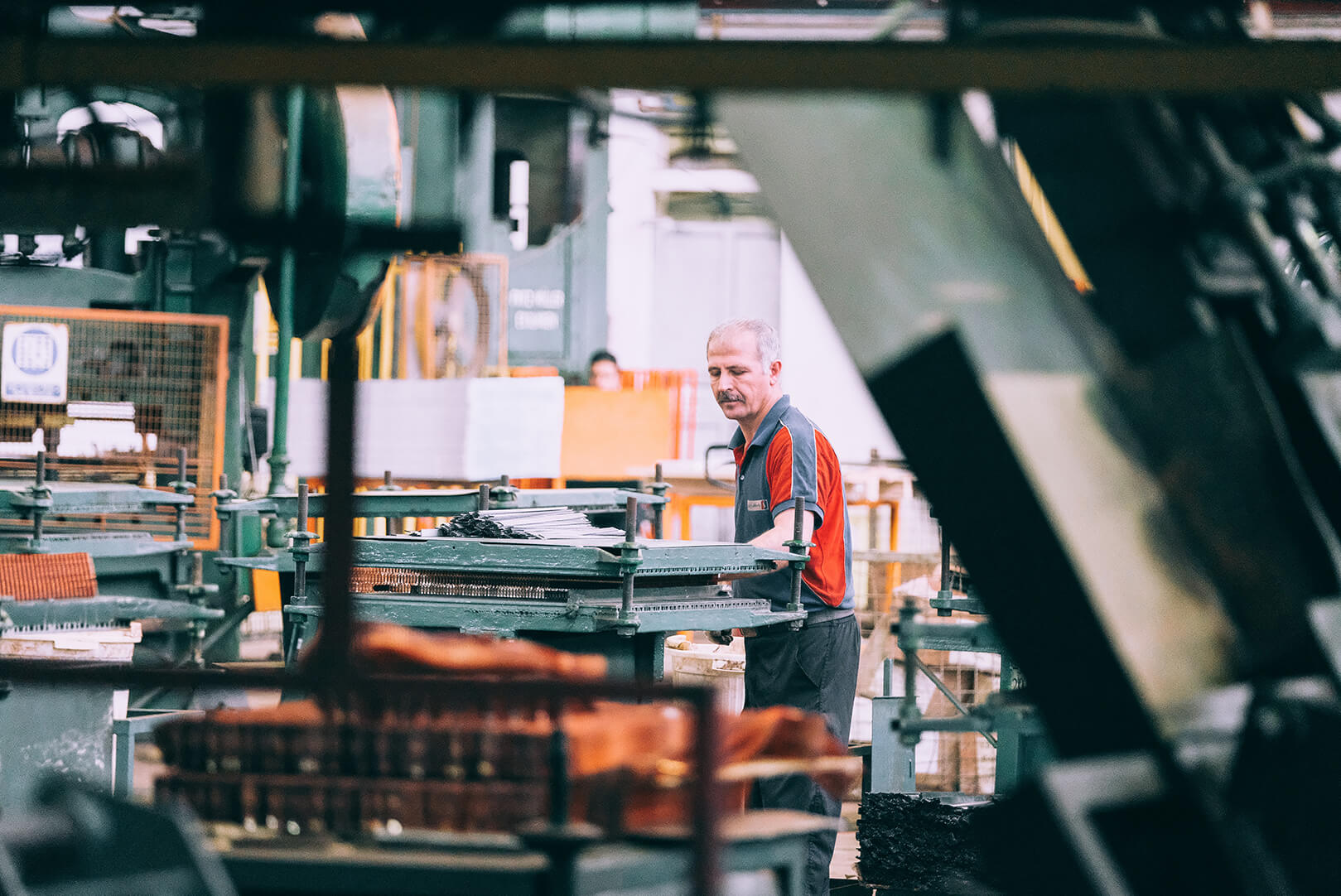
Seiton of Ordenen
Zorg ervoor dat alle items georganiseerd zijn en dat elk item een vaste plaats heeft. Organiseer alle voorwerpen die op de werkplek aanwezig zijn op een logische manier, zodat de werknemers hun taken gemakkelijker kunnen uitvoeren. Dit betekent vaak dat de voorwerpen op een ergonomische manier bereikbaar worden geplaatst zodat men niet hoeft te bukken of te rekken om ze te bereiken.
Enkele vragen om te overwegen:
- Welke mensen gebruiken welke items?
- Wanneer worden de items gebruikt?
- Welke items worden het vaakst gebruikt?
- Moeten de items per type worden gegroepeerd?
- Waar zou het het meest logisch zijn om voorwerpen te plaatsen?
- Zouden sommige plaatsen ergonomischer zijn voor de werknemers dan andere?
- Zouden sommige plaatsen onnodige bewegingen verminderen?
In deze fase moet men als team samen bepalen welke opstelling het meest logisch is. Daartoe moet worden nagedacht over taken, de frequentie van die taken, de loopweg, enz. Welke werkomgeving en opstelling zal het gemakkelijkst werken?
Seiso of blinken
De Shine-fase van 5S richt zich op het opruimen van de werkplek, dat wil zeggen vegen, dweilen, afstoffen, oppervlakken schoonvegen, gereedschap en materiaal opbergen, enz.
Een stralende werkplek lijkt misschien niet belangrijk, maar het is het wel. Meer nog bij 5S neemt iedereen de verantwoordelijkheid voor het opruimen van de werkplek, elke dag opnieuw. Dit zorgt ervoor dat mensen zich eigenaar gaan voelen van de ruimte, wat op de lange termijn betekent dat mensen meer betrokken zullen zijn in hun werk en in het bedrijf.
Naast de basis schoonmaak, omvat Shine ook het uitvoeren van regelmatig onderhoud aan apparatuur en machines. Door onderhoud op voorhand te plannen, kunnen bedrijven problemen opvangen en storingen voorkomen. Dat betekent minder verspilde tijd en minder kosten door schade . Op deze manier kan je met 5S rond de machine naar 5S in de machine gaan. Als je op net iets verder gaat dan 5S algemeen leg je met deze eerste kleine stappen een goede basis en acceptance voor de latere doorstrart naar TPM (TPM total production maintenance)
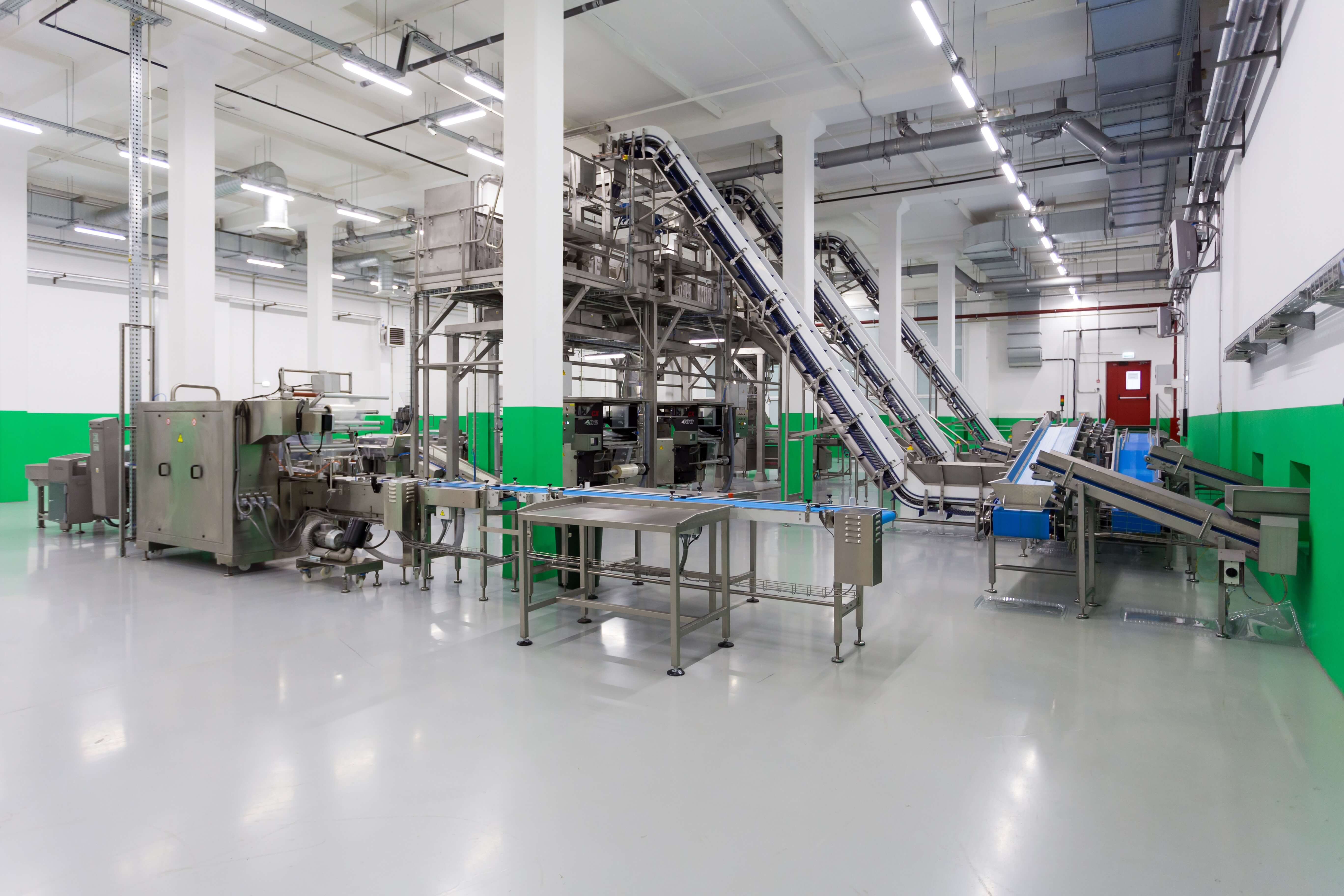
Seiketsu of Standaardiseer
Als de eerste drie stappen van 5S zijn voltooid, ziet alles er uit. Alle extra spullen zijn weg, alles is georganiseerd, ruimtes zijn schoongemaakt en apparatuur is in goede staat. Het probleem is dat wanneer 5S nieuw is in een bedrijf, het gemakkelijk is om op te ruimen en te organiseren... en dan langzaam de dingen weer te laten wegglijden naar hoe ze waren. Standardize maakt 5S anders dan het typische voorjaarsschoonmaak project zoals bv je eigen garage of zolder. Standardize borgt eenmalige inspanningen in gewoontes. Standardize wijst vaste taken toe, maakt schema's en geeft instructies zodat deze activiteiten routines worden. Het maakt standaard werkprocedures voor 5S, zodat 5S niet uit het oog wordt verloren.
Creëer een set van standaarden voor zowel organisatie als processen. In essentie neemt u hier de eerste drie S-en en maakt u afspraken voor hoe en wanneer deze taken zullen worden uitgevoerd. Deze afspraken kunnen schema's, grafieken, lijsten, enz. inhouden.
Afhankelijk van de werkruimte kan een dagelijkse 5S checklist of een schema nuttig zijn. Een opgehangen schema dat aangeeft hoe vaak bepaalde schoonmaaktaken moeten gebeuren en wie er verantwoordelijk voor is, is een ander nuttig hulpmiddel.
Visueel management zoals borden, checklist, labels, posters, vloermarkeringstape, en gereedschaps spelen ook een belangrijke rol in 5S. Ze kunnen aanwijzingen geven en voorwerpen op hun plaats houden, in veel gevallen zonder woorden.
In het begin zullen mensen waarschijnlijk hulp nodig hebben door bv dagelijks een kleine hoeveelheid tijd te reserveren voor 5S taken. Maar na verloop van tijd zullen de taken routine worden en zal 5S organiseren en schoonmaken een onderdeel worden van het dagelijks werk.
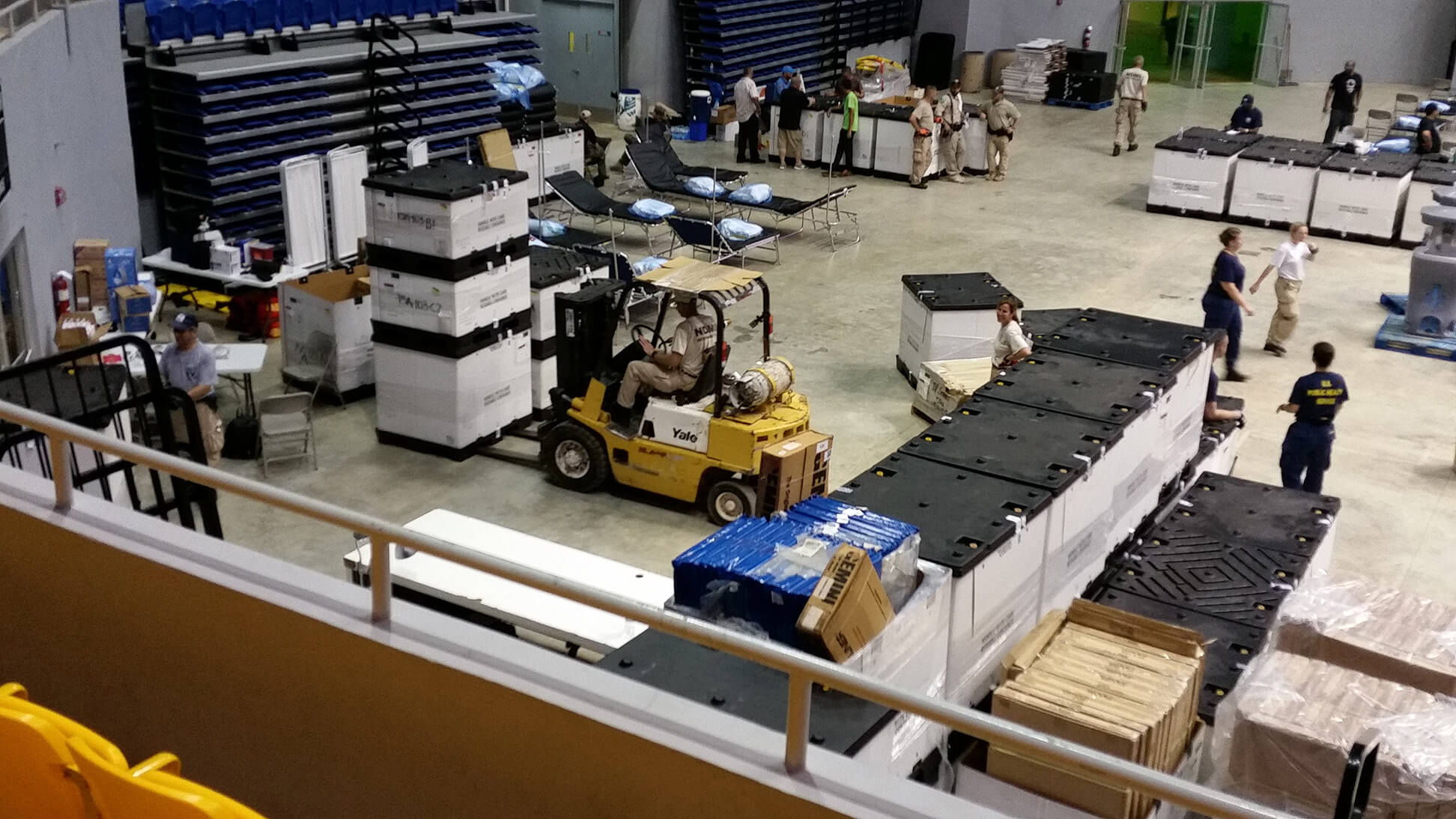
Shitsuke of onderhouden
Als de standaard procedures voor 5S eenmaal zijn ingevoerd, moeten bedrijven de procedures blijven onderhouden en waar nodig bijwerken. Sustain verwijst naar het proces om 5S soepel te laten verlopen, maar ook om iedereen in de organisatie betrokken te houden. Managers moeten deelnemen, net als werknemers op de productievloer, in het magazijn of op kantoor. Het gaat erom van 5S je DNA te maken, niet slechts een actie of kortetermijnproject. En wanneer 5S wordt volgehouden gaat men na verloop van tijd een continue verbetering en fierheid bij medewerkers opmerken .
Veiligheid - De 6e S
Sommige bedrijven voegen graag een zesde S toe aan hun 5S programma: Veiligheid. De veiligheidsstap houdt in dat men zich richt op wat er gedaan kan worden om risico's in werkprocessen te elimineren door dingen op bepaalde manieren te regelen.
Dit kan bijvoorbeeld inhouden dat werkplekken ergonomischer worden ingericht, dat kruispunten - zoals de plaatsen waar vorkheftrucks en voetgangers elkaar kruisen - worden gemarkeerd met borden en dat de opslagkast voor schoonmaakmiddelen wordt geëtiketteerd zodat mensen zich bewust zijn van mogelijke gevaren. Als de indeling van de werkplek of de taken die mensen uitvoeren gevaarlijk zijn, moeten die gevaren zo veel mogelijk worden beperkt. Dat is waar de zesde S zich op richt.
Vervolg
Hoewel 5S een vrij eenvoudig concept is, kan het beginnen met een 5S programma zeer uitdagend zijn. Het is net als de grote schoonmaak in de garage of de kelder thuis; veel werk en niemand vind het nodig ! Het is toch goed zoals het nu is !
Begin daarom met walk the talk en zoek medestanders in afdelingen en personen die erbij betrokken willen worden, geef opleiding en tijd waar nodig. Voorzie hulpmiddelen, gebruikt om het proces te vergemakkelijken. Een goede voorbereiding voor de start zal helpen om je 5S implementatie een succes te maken
Praktisch aanpakken ….wie moet deelnemen aan 5S?
Hier is het korte antwoord op deze vraag: iedereen. Als een afdeling met 5S begint, worden managers en alle andere medewerkers erbij betrokken. Als iemand wordt buitengesloten, kan dit leiden tot verwarring of tot rommel waar mensen geen verantwoordelijkheid voor willen nemen.
Het is mogelijk dat sommige mensen een grotere rol zullen spelen in 5S dan anderen, en dat is prima. Er kunnen 5S-verantwoordelijke zijn die helpen organiseren, ondersteunen bij 5S taken of het introduceren van nieuwe medewerkers. Deze mensen zullen uiteraard veel tijd besteden aan het nadenken over 5S in vergelijking met anderen. Iedereen zou echter regelmatig aan 5S moeten denken. 5S kan aanvankelijk plaatsvinden als een actie, maar idealiter wordt het een onderdeel van het dagelijkse werk voor iedereen.
Het is ook belangrijk om te onthouden dat bedrijfsleiders moeten deelnemen aan 5S zodat medewerkers zien dat 5S er toe doet
Praktisch aanpakken... met opleiding
Iedereen die deelneemt aan 5S activiteiten moet worden opgeleid. Dit kan best met een korte intro en vooral door praktische activiteiten.
Het is belangrijk dat de werknemers begrijpen waarom het bedrijf 5S gaat gebruiken en waarom het belangrijk is. Leer ze de 5S stappen en de reden ervan. Ga nadien met de medewerkers naar de Gemba en eventueel naar een 5S best practice van hoe 5S zou moeten gebeuren . Maar geef ze als team daarna de ruimte om hun eigen weg en manier te vinden hoe ze samen 5S gaan organiseren
5 Praktisch aanpakken... Met visueel management
Een belangrijk onderdeel van 5S is dat het ruimtes schoner maakt en daardoor de werking gemakkelijker te begrijpen is. Dat betekent dat mensen gemakkelijker hun werk kunnen doen. Visuele communicatiemiddelen zoals labels, vloermarkeringen, kast- en schapmarkeringen en schaduwborden kunnen het werken vereenvoudigen. Bovendien kunnen deze hulpmiddelen helpen de werkruimte georganiseerd te houden. Een werkplek die op deze manier gebruik maakt van visueel management wordt vaak een visuele werkplek genoemd.
Enkele veelgebruikte visuele hulpmiddelen in 5S zijn:
Vloer Markering :
Deze tapes kunnen worden gebruikt om werkcellen af te bakenen, de locaties te markeren waar apparatuur of materialen moeten staan Ook helpen ze om gevaarlijke situaties zichtbaar te maken.
Etiketten en borden:
Deze visuals gebruiken tekst, kleuren en symbolen om informatie over te brengen. Ze kunnen de inhoud van laden aanduiden, wijzen op gevaren, of vertellen waar onderdelen moeten worden bewaard.
Schaduwborden en gereedschapskistschuim:
Deze visuals zijn handig in werkruimtes met veel gereedschap. Schaduwborden gebruiken uitsnijdingen van gereedschap die worden geplaatst achter de plek waar een gereedschap aan een bord hangt. Gereedschapskistschuim werkt op dezelfde manier, maar het past in een lade van een gereedschapskist. De vorm van het gereedschap is uitgesneden uit een bovenlaag van schuim, zodat een lichte onderlaag van schuim doorschijnt. Beide methoden benadrukken het ontbrekende gereedschap en vertellen mensen precies waar ze het gereedschap moeten neerleggen als ze het niet meer gebruiken.
Bedrijven kunnen ervoor kiezen om sommige of al deze visuele hulpmiddelen te gebruiken. Ze helpen allemaal om de vaak geciteerde uitspraak van 5S te bereiken: "Een plaats voor alles, en alles op zijn plaats." Deze hulpmiddelen maken duidelijk waar dingen thuishoren, zodat rommel niet zo snel een probleem wordt.
Voor en na 5S
Het zou dan ook geen moeilijke keuze moeten zijn om voor 5S te gaan daar het veel meer is dan opruimen en ordelijk houden. Met tijd , opleiding en een kleine investering in hulpmiddelen zorgt 5S er voor dat afwijkingen gemakkelijker te ontdekken zijn en potentiële problemen snel gezien worden voordat ze uitgroeien tot grote problemen met veel hinder en frustratie. Op lange termijn gaan medewerkers beter samenwerken , samen verbeteren en gaan processen soepeler verlopen Zelfs ongelukken kunnen worden voorkomen en dat alles zijn zaken die bedrijven meestal veel geld besparen en klanten meer tevredenheid geven.