Video beschikbaar voor leden na onze kick-off op 30/03/2022.
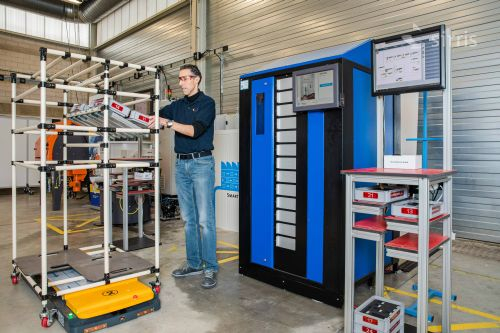
Veel bedrijven stellen vast dat productieoperatoren kostbare tijd verliezen met het wachten op onderdelen of het zoeken naar componenten. Naast een dalende productiviteit zorgt dit ook (en vooral!) voor frustratie bij de operatoren: ze kunnen zich immers niet focussen op hun kernactiviteit, namelijk productie. Er bestaan verschillende strategieën voor het bevoorraden van de productie: de zogenaamde 'material replenishment strategies'.
Elk van deze strategieën heeft een ideaal scenario (bijv. grote reeksen met weinig variatie of high-mix-low-volume-omgevingen) en een aantal voor- en nadelen. In volgende paragrafen gaan we wat dieper in op een aantal veel voorkomende van deze strategieën. Het is belangrijk te vermelden dat in de realiteit vaak elementen uit verschillende strategieën gecombineerd worden. Elke productieomgeving is immers net een beetje anders en vraagt dus een specifieke aanpak. Dit is echter de sterkte van deze strategieën: elementen kunnen - mits wat creativiteit - gecombineerd worden.
Kanban
Een van de meest gekende strategieën voor toelevering van materialen in productie is kanban. Het principe van kanban is vrij eenvoudig: van zodra materiaal nodig is, wordt er een visueel signaal gegeven om extra componenten te produceren (productie-kanban) of aan te leveren (transport- of replenishment-kanban). Kanban is een onderdeel van een zogenaamd PULL-systeem en vrijwaart dat onderdelen enkel geproduceerd (of aangeleverd) worden wanneer ze werkelijk nodig zijn. Bij een kanban-systeem wordt met kanban-kaarten gewerkt. Op dergelijke kaarten staat alle nodige informatie om onderdelen te produceren of aan te leveren:
- Nummer onderdeel (of code)
- Naam onderdeel
- Aantal en eenheid
- Foto (optioneel)
- Type kanban: productie of transport (om fouten te vermijden)
- Verpakking (indien er specifieke eisen gesteld worden aan de verpakking)
- Bron en bestemming
- Indexnummer en totaal aantal kanbans voor dit onderdeel (zo kunnen ontbrekende kanbans eenvoudig geïdentificeerd worden)
Bij het ontwerpen van de kanban-kaarten is het belangrijk om te vrijwaren dat de kaarten duidelijk leesbaar zijn en enkel de noodzakelijke informatie vermelden.
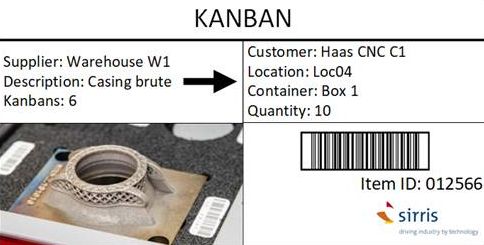
Voorbeeld van kanban-kaarten
In de meeste gevallen bestaat een kanban-systeem uit een mix van productie-kanbans en transport-kanbans. Wanneer een bepaald onderdeel nodig is aan een werkpost, vertrekt de bijbehorende kanban-kaart naar de productiecel (productie van stukken) of magazijn. Het opzetten van een kanban-systeem vraagt wel wat denkwerk over het aantal kaarten, de hoeveelheid werk of producten per kaart, het proces van verzamelen en terugplaatsen van de kaarten, ... Gelukkig is er voldoende informatie beschikbaar in de literatuur om stapsgewijs een kanban-systeem uit te rollen. En belangrijk: continu opvolgen en bijsturen!
Een van de meest gebruikte vormen van kanban is het 'two-bin'-systeem. In de eerste bak (of drager) zit de werkvoorraad en in de tweede de reservevoorraad. Zodra de eerste bak leeg is, wordt de kanban-kaart uit de bak gehaald en als signaal voor herbevoorrading gebruikt (of de lege bak is zelf het signaal voor herbevoorrading). De tweede bak schuift dan naar voren en wordt gebruikt als werkvoorraad. Ondertussen wordt de reservevoorraad aangevuld, zodat het systeem weer in balans komt.
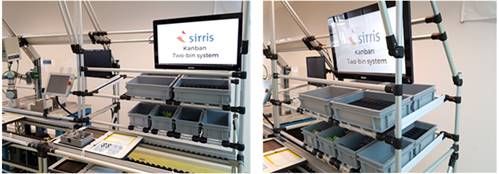
Melkrondes
Milk runs - ‘melkrondes’ - zijn een alternatieve methode voor materiaalleveringen in productie. Zoals de term doet vermoeden, zijn milk runs gebaseerd op de rondes die vroeger uitgevoerd werden voor de levering van melk aan huis. De melkleveranciers vervingen langs hun ronde lege flessen door volle flessen melk. Het aantal lege flessen dat door de klant werd buitengezet, was het signaal voor de melkleverancier om aan te vullen (hetzelfde aantal).
De logistieke milk run loopt gelijkaardig: het is een methode om materiaal uit een centraal magazijn toe te leveren naar de werkposten (of cellen, lijnen) in productie. Milk runs worden vooral toegepast in omgevingen waar men grotere reeksen produceert (met een beperkte variatie aan componenten of onderdelen):
- Een milk run heeft een vaste route met meerdere stops (en eindigt terug aan het startpunt).
- Er is een vast aantal stops op de ronde en aan die stops wordt een lege drager (doos, bakje, …) vervangen door een volle. Er zijn varianten waarbij de aanvulling gebeurt in de volgende ronde: een lege drager wordt meegenomen en bij het volgende bezoek wordt een volle doos met hetzelfde materiaal afgezet. Het aantal stops en aantal componenten dat aangeleverd moet worden, kan vrij eenvoudig berekend worden. Identieke componenten kunnen bijvoorbeeld op meerdere stops aangevuld worden in verschillende aantallen, afhankelijk van het verbruik. Werken met duidelijke labels (zoals bij kanban) reduceert drastisch de kans op fouten.
- Occasioneel kan 'on-demand' materiaal meegenomen worden, maar dit wordt best vermeden om afwijkingen of fouten te vermijden.
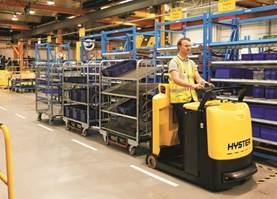
(Bron: www.valuechain.be)
De voornaamste voordelen van milk runs:
- Milk runs zorgen dat willekeurig werk (aanleveren op afroep) gestructureerder kan verlopen volgens een vast patroon. Door een goede planning van de milk run wordt de tijd van de logistieke operator optimaal benut (herhaaldelijke ronde die goed te plannen is).
- De milk run maakt deel uit van een PULL-systeem, wat inhoudt dat materiaal enkel wordt aangevuld bij verbruik en men alzo de voorraden kan beperken, wat dan weer leidt tot minder benodigde ruimte aan de werkposten.
Milk runs hebben één grote beperking: ze zijn enkel geschikt voor grotere reeksen, waarbij een beperkte variatie aan componenten geassembleerd wordt. Wanneer in het productieproces veel maatwerk noodzakelijk is, zijn milk runs hoogstwaarschijnlijk niet geschikt. Kitting (zie verder) is in dat geval beter geschikt: de kits kunnen eventueel wel via een milk run aangeleverd worden.
Kitting
Kitting is een strategie die voornamelijk in assemblagecontext toegepast wordt. Bij het kitten worden onderdelen en componenten (eventueel zelfs pre-assemblies) verzameld en aangeleverd aan de assemblagecel in een 'kit'.
De voornaamste redenen voor het kitten van onderdelen:
- Minder zoektijd (waardoor de operatoren worden ontlast): operatoren moeten niet nadenken over welke onderdelen ze juist moeten assembleren, aangezien ze netjes gegroepeerd aangeleverd worden per product. De zoektijd en de cognitieve belasting voor de operatoren dalen, waardoor ze beter kunnen focussen op het assemblageproces op zich.
- Minder fouten: kitting vermijdt dat onderdelen bij montage worden vergeten. Een kit zet de operator er toe aan om alle aangeleverde delen te monteren. Een poka-yoke-kitbord met uitgesneden vakken voor elk onderdeel (zoals op de foto) kan ook voorkomen dat de kitter onderdelen vergeet aan te leveren.
- Verbeterde organisatie op de werkvloer: door gebruik te maken van kitting wordt het aantal onderdelen dat beschikbaar moet zijn voor de operatoren op de werkvloer verminderd. Dit verbetert niet alleen de organisatie van het magazijn, maar heeft ook een positieve impact op de veiligheid op de productievloer. Immers, door minder onderdelen en materialen op de werkvloer te hebben, komt er ruimte vrij en wordt de kans op een ongeval kleiner.
- Ruimtebesparing: het grootste voordeel dat veel gebruikers van kitting aangeven is de ruimtebesparing aan de assemblagecel of -lijn. Er moeten geen verschillende magazijnen/voorraadzones voorzien worden aan de werkposten, aangezien alles wat ze nodig hebben gegroepeerd geleverd wordt op het juiste moment. Zeker in een high-mix-low-volume omgeving is dit een duidelijk voordeel.
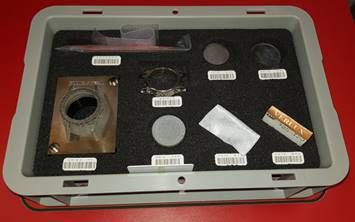
(Bron: Sirris)
Uiteraard zijn er ook een aantal aandachtspunten bij het kitten:
- het opzetten van de kit vraagt onderzoek en planning voor ondermeer het ontwerpen van de kittingcontainer, het bepalen van de eventuele subassemblies, vastleggen van de aanlevering (hoe en wanneer) enz.
- er zal een specifieke kittingzone voorzien moeten worden (bijv. in het magazijn of nabij de assemblagecel) waar de kits voorbereid worden
- het kitten op zich is ook onderhevig aan mogelijke fouten. Het is belangrijk te vrijwaren dat de kittingoperatoren niet belast worden met extra taken en zich kunnen focussen op het samenstellen van de kits. Bijkomend kunnen technologische oplossingen zoals pick-to-light, picking met smartglasses enz. ingezet worden om de kans op fouten te reduceren.
Just in sequence
Just in sequence wordt vooral toegepast in een flow-omgeving. Het principe van just in sequence is vrij eenvoudig: onderdelen en componenten worden in productie geleverd in de volgorde waarin ze nodig zijn. In theorie hoeft de operator niet te kiezen uit verschillende onderdelen, maar neemt hij gewoon het volgende onderdeel uit de wachtrij. Een gekend voorbeeld is assemblage van voertuigen. Vandaag is elk voertuig anders. Bij assemblage van bijvoorbeeld de motorkap, deuren, ... zal men vaak werken met just-in-sequence toelevering, zodat de juiste onderdelen gemonteerd worden.
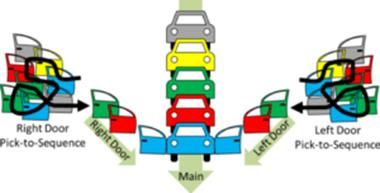
(Bron: www.pyramidsolutions.com)
Het grootste voordeel van just in sequence is een drastische reductie van handling en manipulaties aan de lijn en reductie van zoektijd. De operator dient enkel het volgende onderdeel te nemen en te monteren. Door het ontkoppelen van het picken en monteren verkrijgt men een efficiëntere productie.
De toepassingsmogelijkheden zijn echter, zoals reeds vermeld, eerder beperkt. Men moet immers een vaste volgorde ('sequence') kunnen vastleggen, en deze behouden! Men zit typisch in een flowproductie: assemblagelijn met heel kleine reeksen ('one-piece flow') en veel variatie. De onderdelen die men gaat aanleveren via just in sequence zijn typisch de unieke onderdelen. Men moet zich steeds de vraag stellen of just-in-sequence-aanlevering voor een bepaald onderdeel de zoektijd van dat onderdeel drastisch zou verminderen. Just in sequence is geen strategie op zich en wordt vaak gecombineerd met andere manieren van toelevering zoals kitting of kanban (bijv. voor grijpvoorraad), ...
Vendor managed inventory (VMI)
Vendor managed inventory (vaak ook 'direct line feed' genoemd) houdt in dat de leverancier de voorraad van de klant beheert. De leverancier engageert zich dus om de voorraad van bepaalde onderdelen op een bepaald niveau aan te houden (en dus tijdig bij te vullen).
De belangrijkste voordelen van VMI voor de klant (i.e. het productiebedrijf) zijn reductie van de eigen voorraad en verhoogde beschikbaarheid van de onderdelen/componenten. Inderdaad, doordat de leverancier verantwoordelijk is voor het aanhouden van de voorraad, kan het productiebedrijf de voorraadniveaus reduceren, veiligheidsvoorraden elimineren, aankoopkosten verminderen, ... In veel gevallen is ook de aankoopprijs lager, doordat er veel minder administratie aan te pas komt.
Een van de grootste nadelen van VMI betreft het gedeeltelijk uit handen geven van het aankoopproces. Bij VMI krijgt de leverancier immers toegang tot alle nodige informatie over het reële verbruik van de goederen. Als productiebedrijf geeft u in dit geval dus uw leverancier toegang tot bepaalde bedrijfseigen data. Dit wordt door supply-chain-managers - samen met het risico te afhankelijk te worden van één welbepaalde leverancier - als voornaamste nadeel van VMI gezien.