Video beschikbaar voor leden na onze kick-off op 30/03/2022.
Theuma wil klaar zijn voor de toekomst en zet daarom vol in op Lean of Continuous improvement en problem solving. Na geïnspireerd te zijn in het Lean lead netwerk van lean believers starten we met de hulp van Lean Lead om de productie naar een hoger niveau tillen. Dit door methodes te leren gebruiken zoals A3 thinking en 5 why’s . Vervolgens hebben we op basis van deze nieuwe inzichten en met betrokken medewerkers TPM gaan implementeren met als doel efficiënter, vlotter en kwalitatiever te werken.
Vooruit denken
Theuma een deurenfabrikant die vooruit wil denken en een stap voor wil zijn op de problemen van morgen. Hierbij willen we dit doen samen met alle medewerkerkers want alleen zo kan men een goed resultaat behalen. Door de samenwerking met Lean Lead werden ons manieren aangeleerd die we in de toekomst kunnen gebruiken om problemen snel op te lossen of ze zelfs te voorkomen. Dit vooral rond kwaliteit en beschikbaarheid. Ikzelf , continuous improvement coördinator , Stoffel Guerry stond op de eerste rij van deze lean transformatie en neem jullie graag mee in onze leerervaring en zal hier graag mijn ervaring delen.
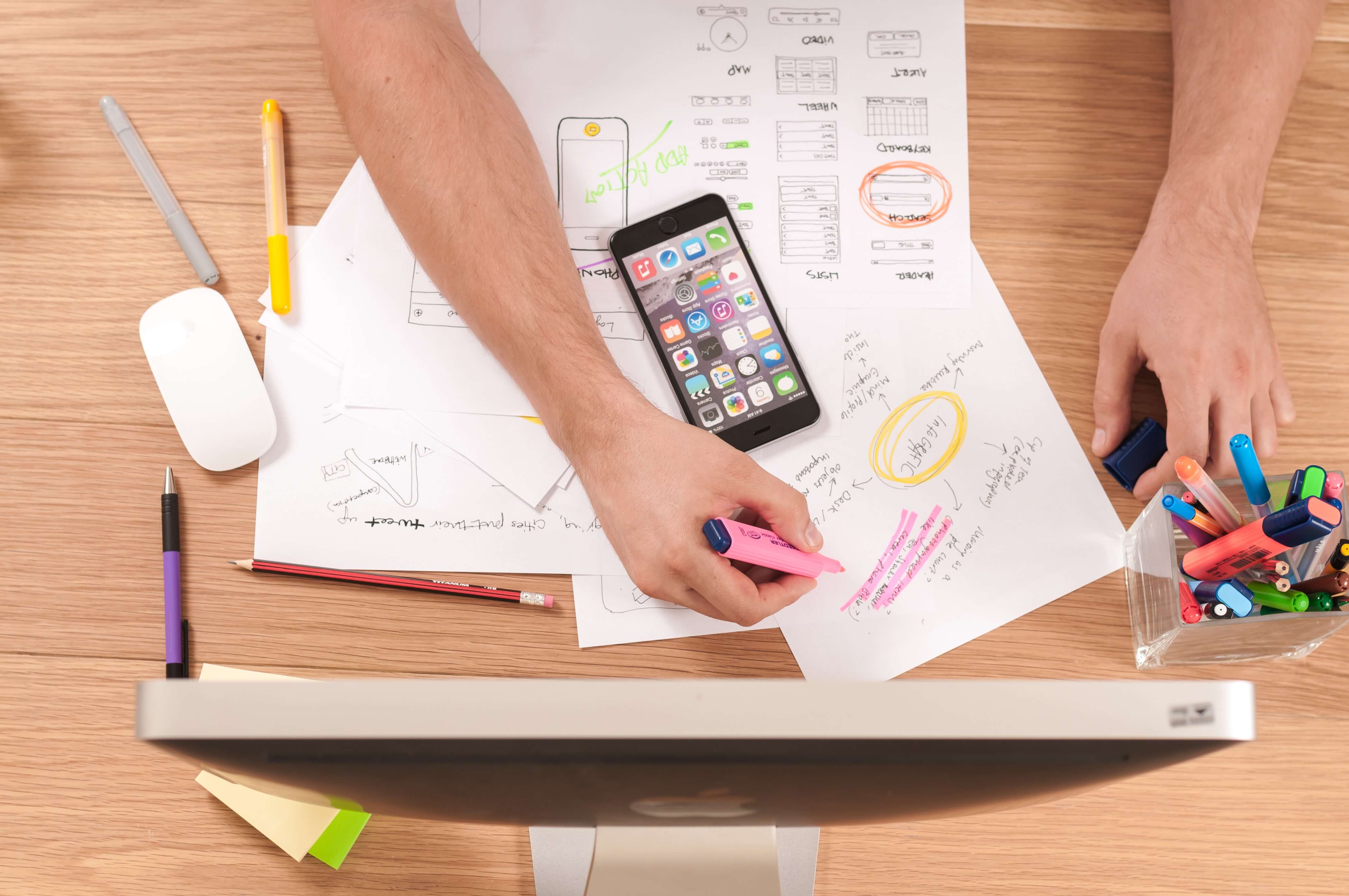
A3 thinking
Deze ervaring en case gericht opleiding over A3thinking zorgde ervoor dat alle teamleaders en verschillende arbeiders aan de slag gingen in drie teams en voor het eerst in contact kwamen met deze manier van werken en denken. Door de A3 thinking methode te gebruiken hebben we tijd gemaakt om de uitdaging/probleem te beschrijven, het probleem uitvoerig met feiten en cijfers te analyseren en vooral te luisteren naar de issues van de arbeiders. Zo kan je hen mee betrekken in het verbeteren en problem solving . Dit is volgens mij dan ook de belangrijkste factor want door deze betrokkenheid van de mensen op de werkvloer, gaat de snelheid waarmee ze reageren , actie ondernemen etc. verbeteren.
We gaan zo sneller ingrijpen “Quick respons” als er een probleem zich voordoet en ook snel kunnen handelen en de impact beperken. Verder is een goede analyse zeer belangrijk wil je niet alle effort steken in het verkeerde waardoor je je doel dat voorop vastgelegd werd niet kan halen.” Wat wel een valkuil was waar we zeker problemen mee hadden is ‘jumping to conclusion’ waarbij we een probleem vaststellen en direct allerlei acties ondernamen. Wat dus neer komt dat we de analyse overslagen en direct op het door ons gedachte probleem springen. Tip , doe steeds een stap achteruit en denk in een klein team even na samen met bv arbeiders en onderhoudsmedewerkers. Dit werkt voor ons heel goed en wordt vandaag de dag nog gebruikt.
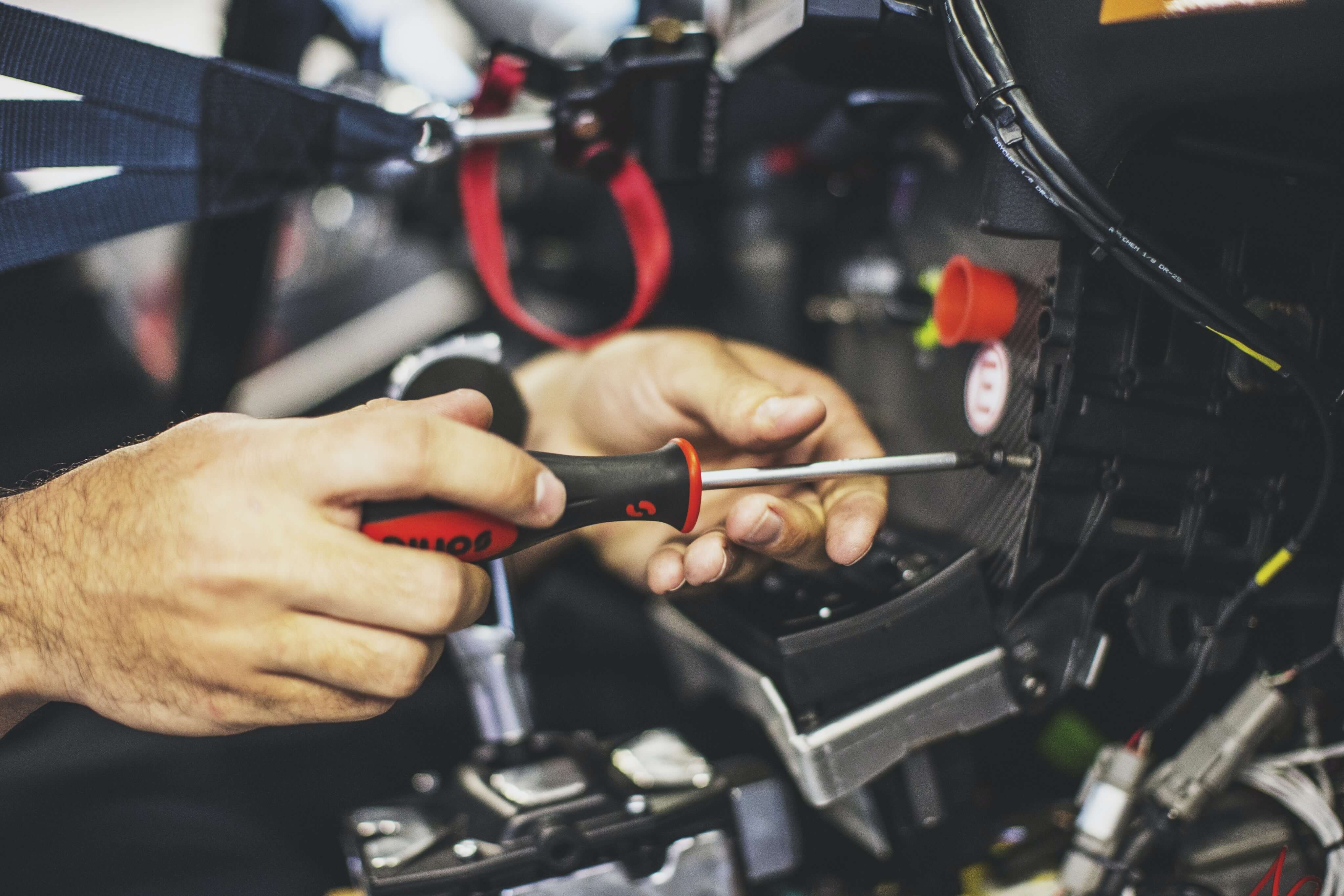
Doelen haalbaar?
Vaak opgelegde “Doelen & KPI’s” lijken soms onhaalbaar als je begint aan een project van verbeteren. Ook voor ons team was dit niet makkelijk maar ondertussen zeg ik : “Don’ t worry and go with the flow” Stel voor je team kleine doelen voor waar je in gelooft en in kleine stappen naar werkt .Geniet dan vooral van de ervaring en de kleine verbeteringen die je behaalt als team. In het begin heb je zeker mensen tegen bij het implementeren van deze verbeterprojecten omdat deze tijd en effort vragen. Na verloop van tijd zullen zij ook inzien dat het makkelijker werkt en zullen ze met plezier meewerken in het project en de volgende.”
TPM meer werk? Dacht het niet!
TPM lijkt voor velen extra werk, dit is het ook enkel bij de kickoff ervan daarna bespaar je zoveel werk uit en heb je veel minder problemen. TPM helpt het verminderen van ongeplande stilstanden en pannes zodat we continu kunnen produceren zoals we zelf plannen.
Zelf zitten we bij Theuma nu met drie afdelingen die al werken met TPM . Waarom nog maar drie zou je kunnen afvragen, simpel alles tegelijk kan niet. Begin bij het begin en laat het groeien binnen je bedrijf. Ook hierbij hang je heel hard af van de betrokkenheid van de mensen. Ook hier is het van belang dat je ze uitlegt en samen laat ontdekken dat het makkelijker en aangenamer werken is. Luister naar hun opmerkingen, help en ondersteun hen bij deze problemen want zo voelen ze dat ook hun mening belangrijk is en dat aan hun problemen worden gewerkt & opgelost.
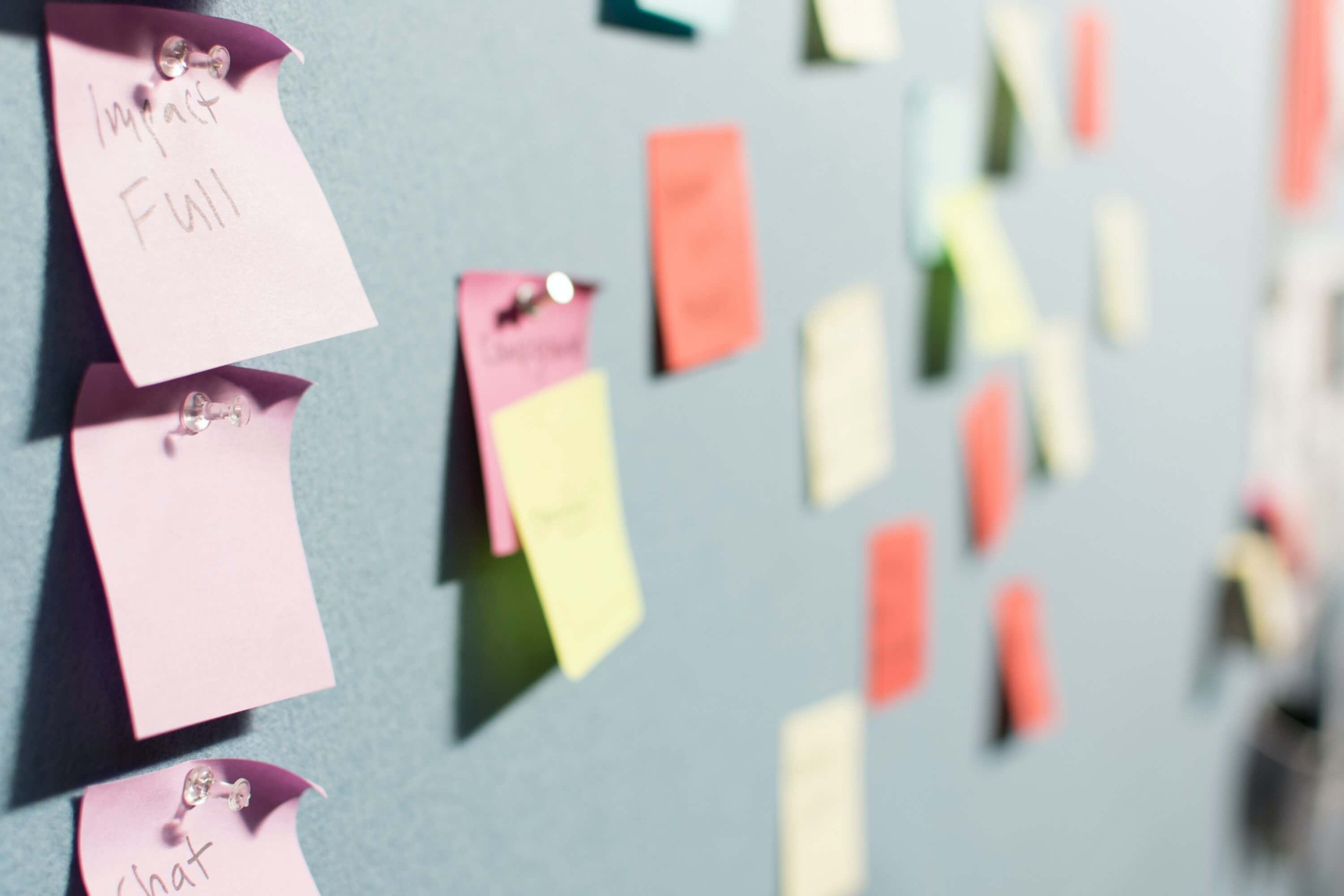
Nu geen pannes meer?
Het onderhoudsteam vindt TPM ook een betere methode omdat ze gepland tijd krijgen om problemen op te lossen. Waar het voordien vaak was van produceren tot het defect gaat en de daarbij horende ongeplande stilstand. Deze dient dan weer snel gemaakt te worden zonder voorbereidend werk, veel problemen en uitdagingen voor het team . Hierdoor ontstaat er meer druk bij hun en vaak duurde het lang om iets te repareren. Dit wil niet zeggen dat er geen ongeplande pannes meer zijn maar het is zoveel gebeterd dat het aangenamer werkt.
Voldoening en plezier
Wat vaak vergeten wordt : alle mensen op ieder niveau willen ook voldoening en plezier uit hun werk halen. Dit is ook nodig zodat mensen gemotiveerd mee werken aan verbeteren. Dus geniet van de kleine en grote vooruitgangen die je maakt met jullie team, ongeacht de gebruikte methode.
Dit artikel werd gerealiseerd in samenwerking met Stoffel Guerry van Theuma.