Video beschikbaar voor leden na onze kick-off op 30/03/2022.
MCT - praktische tool voor visualisatie van tijd
Doorlooptijdverkorting start met het in kaart brengen van de doorlooptijd. De MCT vormt een handige tool waarmee je de doorlooptijden overzichtelijk kan maken. Het verkorten van de doorlooptijd biedt tal van voordelen. Zo leidt doorlooptijdverkorting tot een verlaging van de voorraden, minder plannings- en coördinatiewerk, hogere leverbetrouwbaarheid, een hogere klantentevredenheid en finaal minder chaos en stress.
Het begrip 'doorlooptijd' is echter een vlag die vele ladingen dekt. Sommigen interpreteren doorlooptijd als de levertijd voor de klant, de ingestelde tijden in het ERP-systeem, de tijd van goederenontvangst tot verzending, de tijd van bestelling tot facturatie,… Het reduceren van elk van deze tijden is op zich interessant, maar niet alle doorlooptijdverkortingen hebben evenveel impact. Voor make-to-stock-bedrijven is de levertijd al erg kort, waardoor het verder verkorten van die levertijd niet veel impact zal hebben. Daarentegen kan bij make-to-stock-bedrijven de tijd van goederenontvangst tot verzending erg lang zijn, doordat producten erg lang in het magazijn verblijven. Het verkorten van deze laatste doorlooptijd zal wel veel impact hebben.
MCT
Het correct definiëren van de doorlooptijd is essentieel wil men impact hebben met het verkorten van de doorlooptijd. Daarnaast kan een goede definitie ook spraakverwarring en misverstanden vermijden. Een heldere en breed toepasbare definitie voor de doorlooptijd is de Manufacturing Critical-path Time (MCT).
De Manufacturing Critical-path Time (MCT) is gedefinieerd als 'de typische hoeveelheid kalendertijd vanaf het moment dat een klant een order plaatst, langsheen het kritieke pad, tot het moment waarop de klant het eerste (complete) eindproduct ontvangt'. Simpelweg gezegd komt dit neer op de tijd om vanaf niets een product te maken tot de levering bij de klant. Laat ons voor de duidelijkheid de definitie even ontleden:
- de typische hoeveelheid kalendertijd:
We gaan onszelf niet rijk rekenen door te kijken naar het beste geval, maar kiezen voor de typische waardes. Een manier om die in kaart te brengen is door te kijken naar de gemiddelde waardes. In de praktijk zijn gemiddelde waardes vaak niet zo representatief, omdat ze vertekend worden door registratiefouten die typisch opduiken als zeer kleine getallen (nul) of zeer grote getallen. Een betere manier is daarom om de mediaan te berekenen. De mediaan wordt minder vertekend door de extreme waardes. We rekenen ook in kalenderdagen en houden dus geen rekening met weekends en verlofperiodes. Voor de klant maakt het immers niet uit wanneer je werkt, hij zit te wachten op zijn product. - langsheen het kritieke pad:
Producten zijn frequent opgebouwd uit meerdere componenten die elk een andere weg afleggen. Het kritische pad komt overeen met het langste tijdspad om vanaf niets een product te maken. Het kritische pad doorloopt alle stappen die nodig zijn om de componenten te produceren. Je mag dus niet vertrekken vanaf de eventueel op voorhand geproduceerde onderdelen. De tijd in de voorraad wordt eveneens meegeteld. Niet-kritische items (zoals bouten, verpakkingsmateriaal, …) worden voor de eenvoud niet meegenomen in de berekening. Deze items vertegenwoordigen typisch een lage waarde, waardoor het niet de moeite loont om die op te volgen. - het eerste (complete) eindproduct:
Dit deel van de definitie laat deelleveringen toe en moedigt werken in kleinere loten aan. Als een klant slechts eenmaal per jaar 50 stuks bestelt, dan verbruikt hij wellicht ca. 1 item per week. Wellicht volstaat het dus om 1 item per week te leveren. Kleinere leveringen en productieloten zijn een belangrijke techniek om de doorlooptijd kort te houden. De toevoeging 'compleet' garandeert dat de levering aan de klant ook bruikbaar is voor de klant. Voor een bandenproducent betekent dit bijvoorbeeld dat een levering aan een autoproducent minstens vier banden omvat, omdat een auto nu eenmaal 4 banden nodig heeft om compleet afgewerkt te kunnen worden.
MCT-map
De MCT kan ook worden gevisualiseerd in een overzichtelijke kaart: de MCT-map. De onderstaande figuur toont een voorbeeld van een MCT-map. De kaart toont de opeenvolgende processtappen en de samenhang van de componenten (de takken in de map) die vervolgens bij de assemblage-tak samenkomen. De tijdsblokken hebben twee kleuren: wit wordt gebruikt om de wachttijden te visualiseren; grijs visualiseert de tijd die nodig is om het eerste deel te produceren.
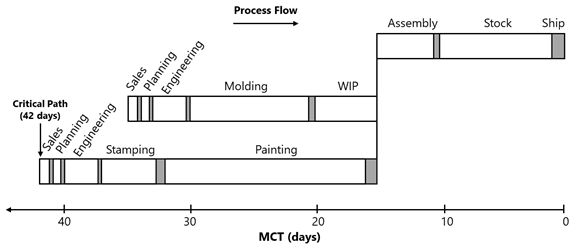
De grijze tijd omvat zowel de omsteltijd als de eigenlijke productietijd van het eerste (complete) deel, dus niet de productietijd van het gehele lot. Bij lotproductie is men typisch één deel aan het produceren, terwijl de andere delen van het lot aan het wachten zijn. De grijze tijd is typisch slechts 5 procent of minder van de MCT. Het overgrote deel van de MCT is dus witte tijd. Anders geformuleerd: in de meeste bedrijven wachten de orders gedurende 95 procent van de tijd op een bewerking. Dit duidt aan dat er nog heel wat marge tot verbetering is. Een doorlooptijdverkorting van 50 procent of meer is daarom geen uitzondering.
Een MCT-map heeft meerdere voordelen:
- De MCT-map is eenvoudig en niet overladen met gegevens. Hierdoor is de MCT-map gemakkelijk door iedereen te begrijpen.
- Het visuele karakter van de MCT-map toont duidelijk de verhouding tussen de witte en grijze ruimte, en onderlijnt zo het grote potentieel voor doorlooptijdverkorting. Het maken van een MCT-map is daarom vaak een eye-opener.
- De verbeteropportuniteiten vallen onmiddellijk op. Zo is op de MCT-map duidelijk te zien dat de grootste wachttijd zich bevindt voor de stap 'painting'. De tweede grootste verbeteropportuniteit is de 'stock'.
- De MCT-map maakt het kritische pad onmiddellijk duidelijk. Zo valt op dat het verkorten van de witte wachttijd voor 'molding' in eerste instantie de MCT niet zal verkorten. Verbeteringen zullen op het pad 'stamping/painting' en 'assemblage' moeten liggen om een impact op de MCT te kunnen hebben.
- De MCT vat de performantie van het volledige systeem mooi samen in één getal, wat zorgt voor een duidelijke focus op bedrijfsbrede verbeteringen. De MCT is een metriek die daarmee continue verbeteringsprojecten goed ondersteunt, omdat het de totale systeembrede verspilling van een organisatie kwantificeert.
Om de bruikbaarheid van de MCT-map te verbeteren gelden twee bijzondere regels. Een eerste bijzonderheid is dat de kantoorstappen (sales/planning/engineering in de figuur) in de beide componenttakken voorkomen. Een tweede bijzonderheid is de richting van de as die georiënteerd is van rechts naar links. Hierdoor wordt het gemakkelijker om de impact van verbeteringen in te schatten. Als we in de bovenstaande MCT-map de wachttijd van de stap 'painting' zouden elimineren, dan zien we dat het kritische pad zich zou verplaatsen naar de tak met 'molding'. Door de kantoorstappen in beide takken te herhalen verliezen we die niet uit het oog en door de asoriëntatie kunnen we snel aflezen dat de nieuwe MCT 35 dagen wordt.
Opstellen van een MCT
De MCT en de MCT-map zijn eenvoudige tools waarmee snel inzicht kan worden verkregen. Een eerste ruwe versie van een MCT-map kan veelal op een uurtje worden geschetst op een bord door de betrokken personen samen te brengen. De grijze tijden zijn meestal wel bekend bij de betrokkenen, over de witte wachttijden kan er soms wat twijfel zijn. Hiervoor zal soms wat bijkomende data moeten worden verzameld. Bij sommige bedrijven zijn er tijdsregistraties terug te vinden in het MES- of ERP-systeem en kunnen de wachttijden worden ingeschat op basis van het verschil tussen starttijd van een order op één stap en de afmeldtijd van dit order op de vorige stap.
Een andere eenvoudige manier is door het tellen van de 'Work In Process' (WIP). De wachttijd kan dan worden berekend door de WIP aan een stap te delen door de doorvoersnelheid ('throughput'). Een voorbeeld: als aan een stap 200 items liggen te wachten en er worden gemiddeld 50 items per dag verwerkt, dan is de doorlooptijd 200/50 = 4 dagen. De doorvoersnelheid komt overeen met de gemiddelde verkoop per dag plus de scrap. Het scrappercentage is doorgaans erg laag en kan gemakshalve verwaarloosd worden. Houd er wel rekening mee dat de WIP sterk kan variëren van dag tot dag. Je telt daarom best op meerdere dagen de WIP om zo tot een betrouwbaar gemiddelde te komen.
Een derde manier om de doorlooptijden in kaart te brengen is door 'tagging'. Dit is een manueel registratieproces waarbij men gedurende een tijd bijhoudt wanneer een order in een stap aankomt en wanneer het order de stap verlaat. Hiervoor wordt typisch gebruik gemaakt van papieren registratieformulieren die door de medewerkers worden ingevuld.
Tools voor het opstellen van een MCT-map
Voor het maken van mooie MCT-plaatjes kan je de data zelf visualiseren met behulp van Office-tools zoals Excel of kan je een beroep doen op specifieke softwaretools voor het visualiseren van de MCT-map.